EPICALS TJÄNSTER
TPM
Total Productive Maintenance (TPM) – Ensuring Reliable Equipment for Increased Profitability and Improved Processes
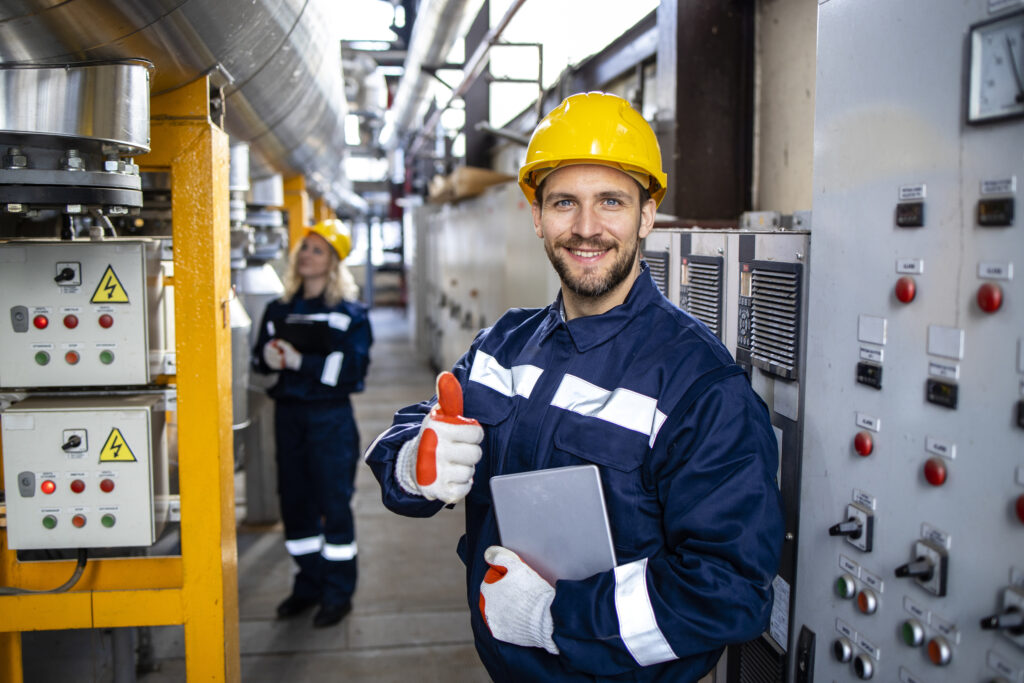
Total Productive Maintenance (TPM) aims to produce with reliable equipment at high capacity and the right speed, which increases profitability and creates conditions for further developing production processes. This requires the entire organization to be involved in reliability work to create disturbance-free processes by introducing operator maintenance, where production personnel are trained and take over certain maintenance tasks such as inspections, lubrication, and simple repairs. The maintenance department uses the time freed up to develop specialist maintenance, which involves planning restorative, improving, and modifying activities based on production conditions and the company's goals & vision, and systematically developing standardized work methods and being involved early in new acquisition projects to ensure equipment reliability. Specialist maintenance also means becoming a learning organization by training operators in maintenance and maintenance techniques and creating internal instructions and training. TPM is also a culture of continuous improvement and shared responsibility for the loss model (OEE) within the organization.
The following results can be achieved by implementing TPM
- Increased Efficiency (OEE) Reduced number of breakdowns through increased care and inspection by the operator, and specialist maintenance that prevents, plans, and improves machine efficiency.
- Reduced costs: Manufacturing and maintenance costs decrease, as well as capital tied up in work-in-progress (WIP) and finished goods inventory.
- Increased quality: Scrap and rework, as well as customer complaints, decrease.
- Increased delivery reliability: Despite reduced finished goods inventory, delivery reliability also increases.
- Increased safety: The number of accidents decreases, but the awareness to report incidents increases.
- Increased morale: As operator maintenance, 5S, and improvement work increase involvement, morale is boosted, and the number of improvement suggestions will also increase drastically.
- Freeing up resources: Resources are freed up as disruptions decrease, allowing resources to transition to developmental/strategic tasks such as improvement work and participation in new acquisition projects.
- Lifespan The lifespan of equipment is extended through increased care and proper preventive maintenance.
TPM's Layout
Based on the need to improve operational reliability, we provide assistance within the entire TPM methodology. The goal is to measure and understand machine losses (OEE) and reduce these, as well as to develop maintenance in the following areas:
- Operator Maintenance
- Specialist Maintenance
- Competence Development
- Continuous Improvement
- New Acquisitions
- Quality Maintenance
- TPM Administration
- Safety, Health, and Environment
Depending on the need for development, this will be done through our developed best practice solutions/methods, templates, tools, system solutions, training, digital solutions and visual solutions from visuellafabriken.se
What Losses and Wastes Do You Suffer From?
Planned losses
95%
Breakdown
90%
Changeover losses
85%
Tool change
80%
Speed losses
75%
Short stops
70%
System losses
65%
Scraps
55%
Rework
45%
Wastes
35%
Involvement
25%
Security
15%
Environment
5%
Project Group Participants
Chefer, ledare, tekniker, operatörer, montörer, administrerande personal" translates to "Managers, leaders, technicians, operators, assemblers, administrative staff
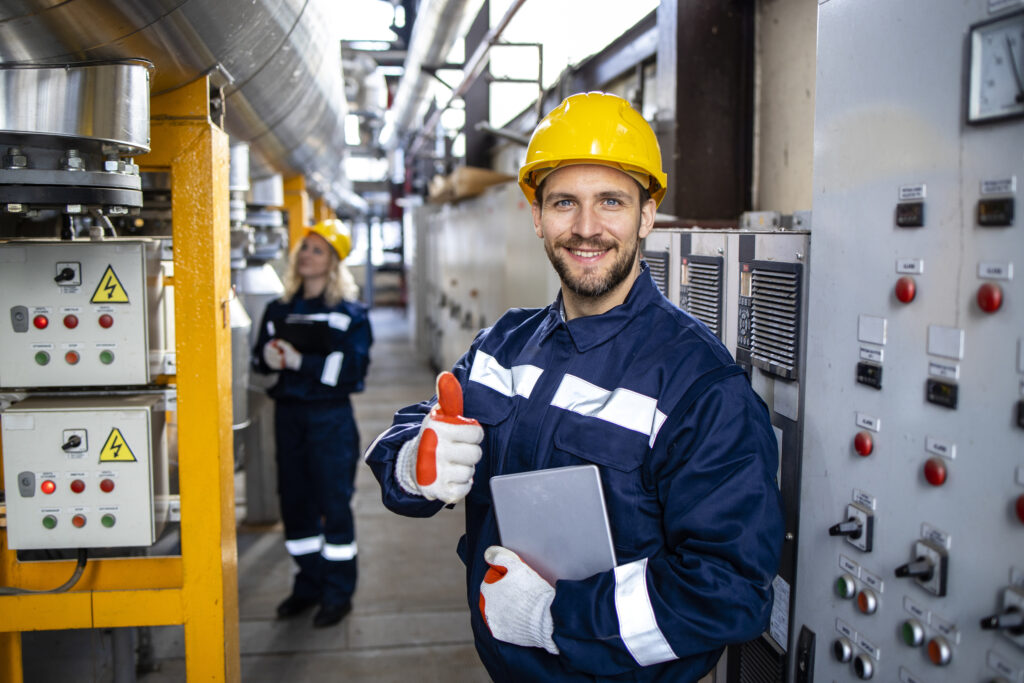
Contact Us
Contact Us
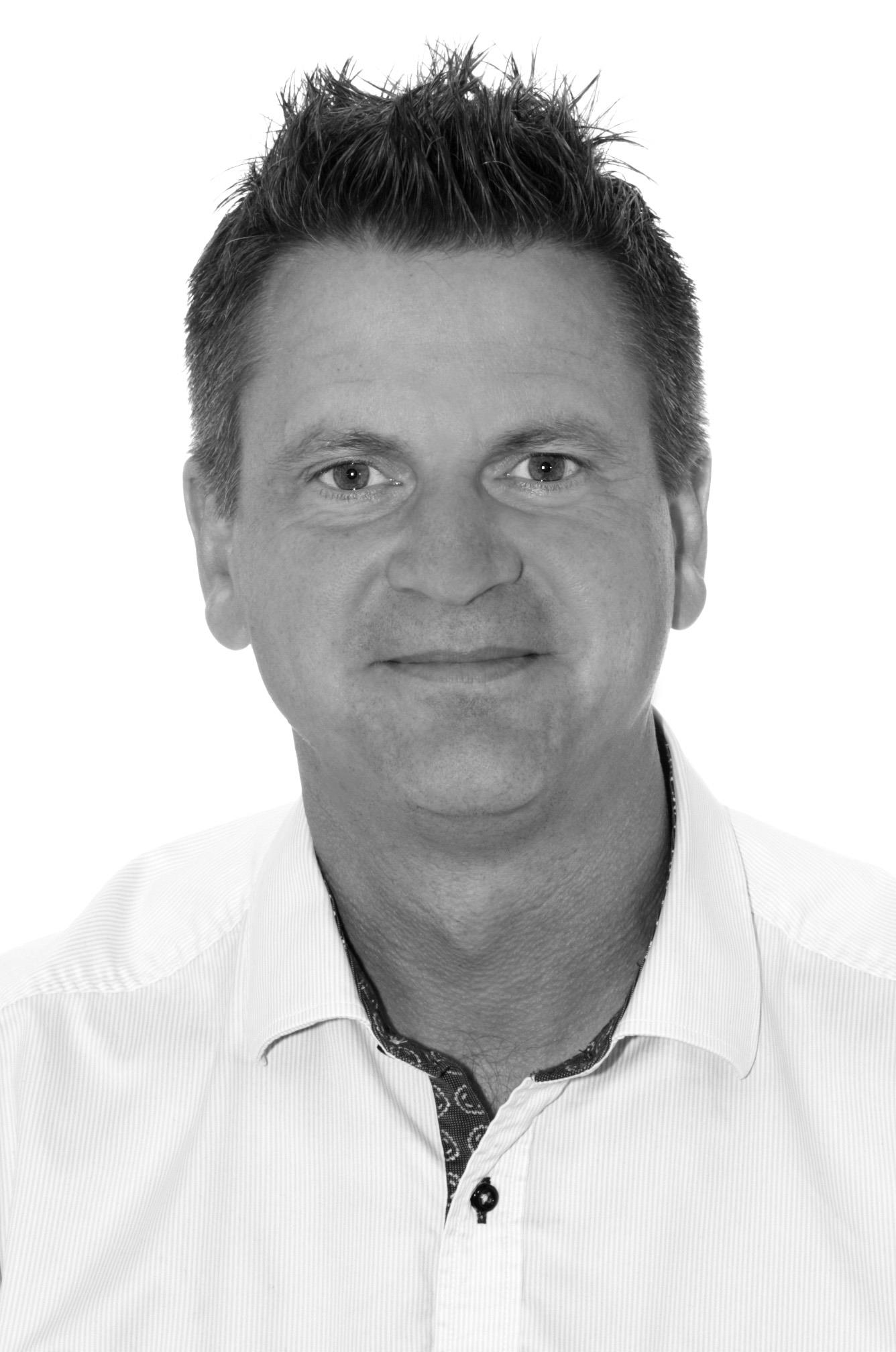
Håkan Östholm
Sales and Senior Business Consultant
Phone
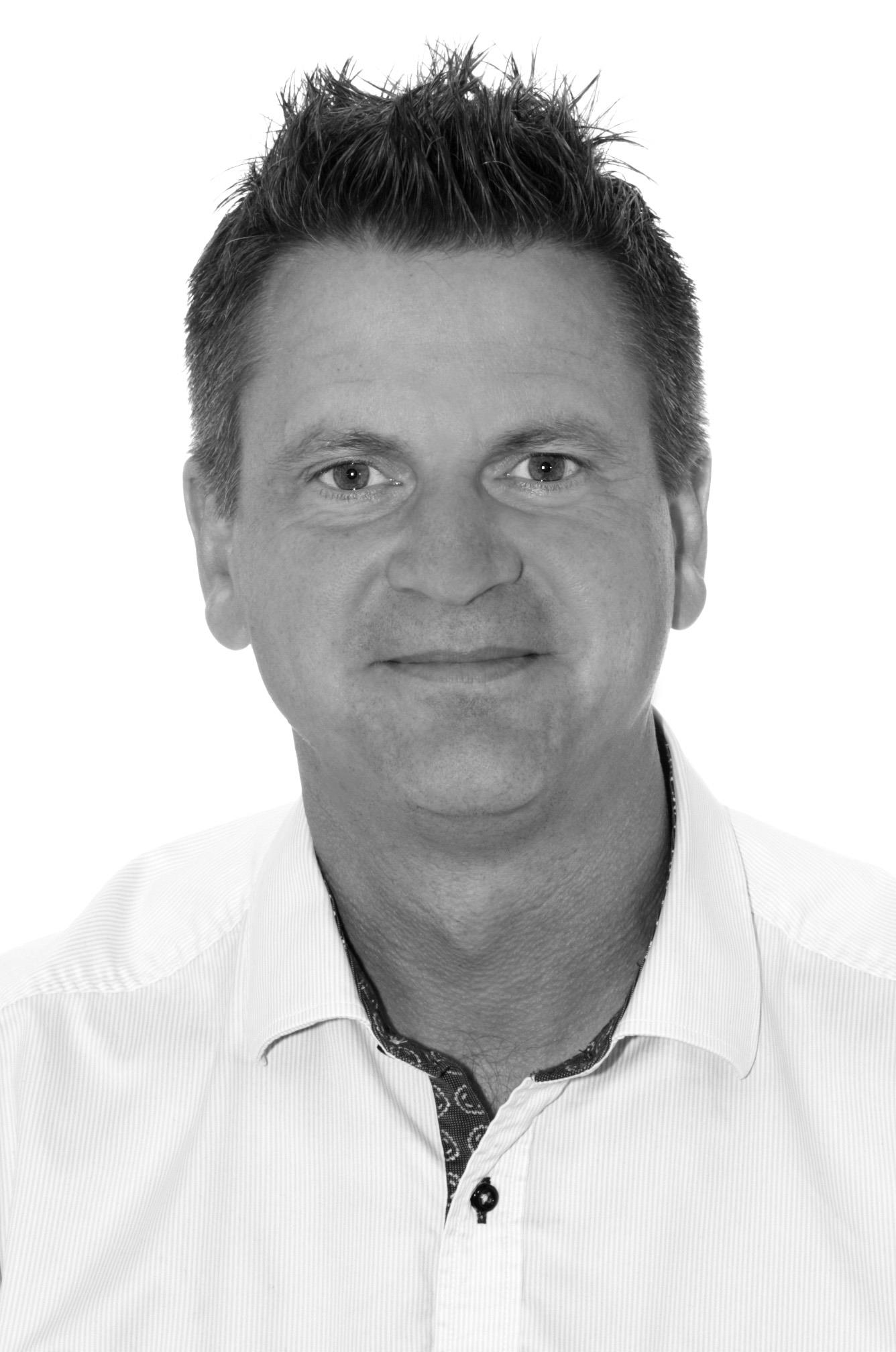