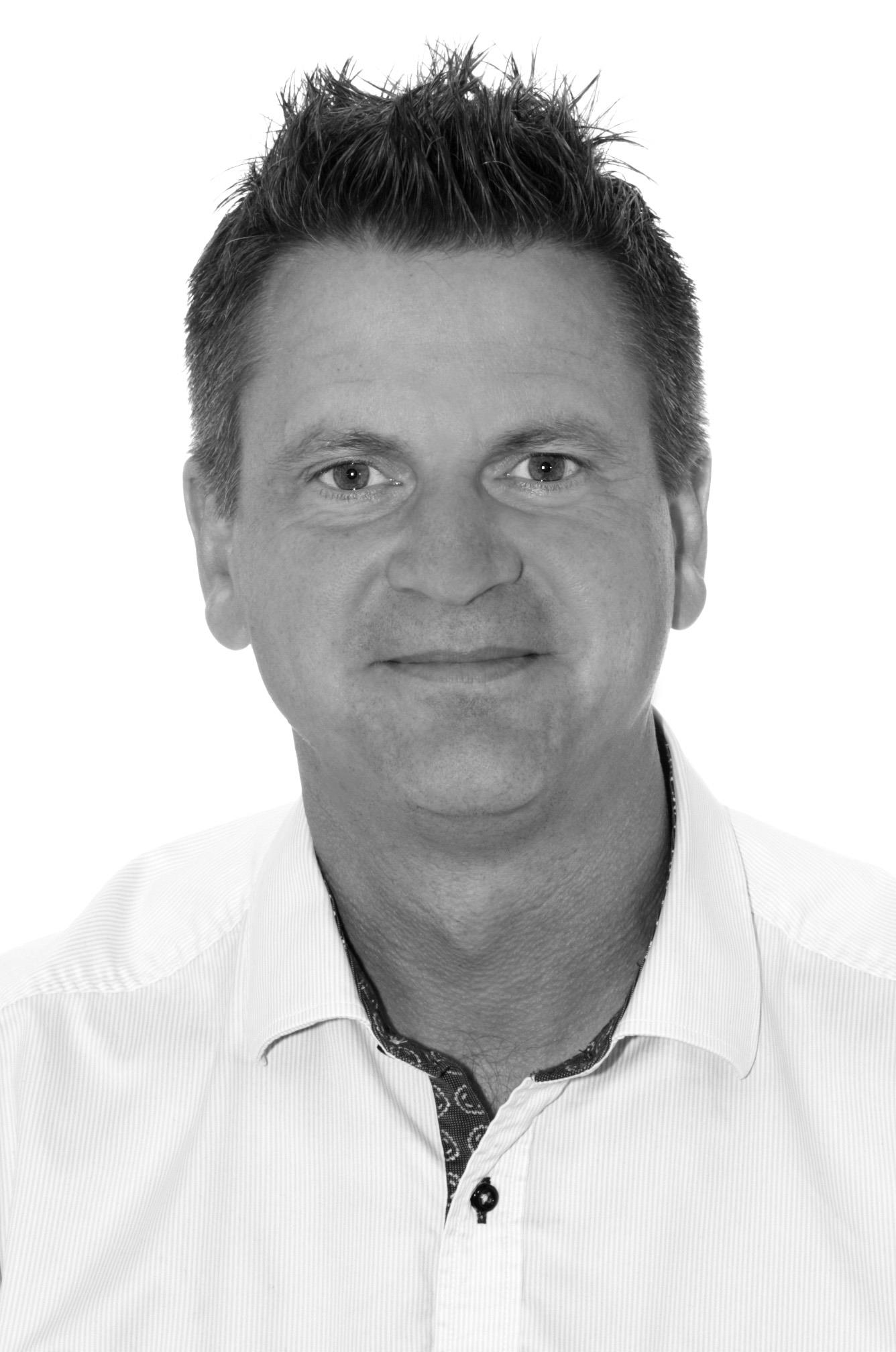
EPICALS TJÄNSTER
Standardization
Home > Standardization
Effective Standardization for Success
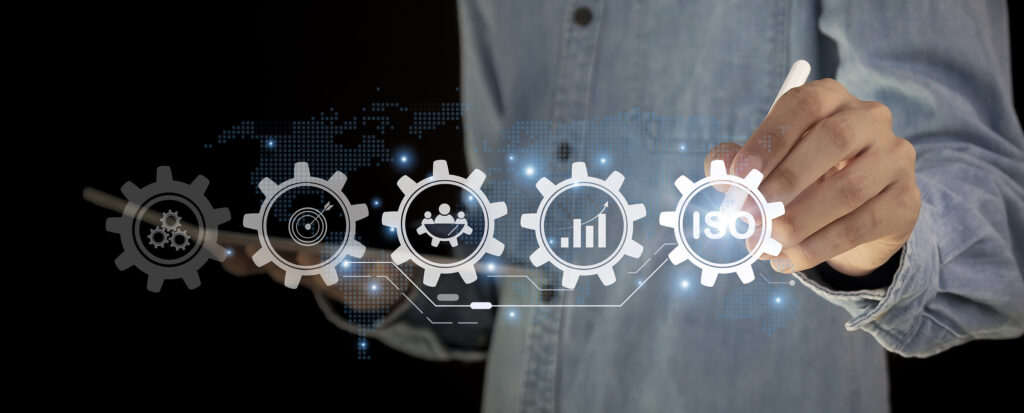
Standardizing a process has several benefits that can help improve efficiency and quality in an organization. Here are some of the key reasons:
- Cost-effectiveness: Standardization helps create cost-effective processes by reducing variations and inefficiencies.
- Consistency and Quality: By standardizing processes, you ensure that work is performed the same way every time, leading to high and consistent quality.
- Security: Standardized processes can help enhance safety by establishing clear guidelines and procedures that everyone follows.
- Compatibility and Credibility: Standardization ensures that different parts of the organization work well together and can increase credibility both locally and globally.
- Facilitates Training and Procurement: With standardized processes, it becomes easier to train new staff and conduct procurements, as everyone knows exactly what is expected.
- Support for continuous improvement: A standardized process provides a stable foundation for identifying and implementing improvements.
- Support for Leadership: If the process is standardized, it provides strong support for leadership to support, coach, follow up, analyze, and guide the organization to success.
To facilitate this process, you can also explore our range of products that help streamline and support implementation. See our solutions at Visuellafabriken.se.
Structure of Standardization
If the process is not known to us, we first map the process in workshop form where Epical asks questions and maps out the process to then standardize it. The role of the workshop participant is to be active in the workshop to answer questions, suggest process improvements, and review the documented process. If the process is known to us, we use our developed best practice library where we start from our process and then find the customer's adaptation. The joint work is to find the optimal adaptations based on needs/requirements, organization, support systems, and conditions.
- Based on a design intended to handle optimal implementation, support in leadership, and future updates
- Describes the process in text form after process mapping through a process instruction
- Describes the handling of support systems in the process through an operating instruction
- The standard is converted into a handbook, informational material, and training material.
- Educational material is converted to E-learning
Who Participates in Standardization
Managers, leaders, and invited participants who have insight into how the process is conducted
Scope and Content of Standardization
1 workshop day and 1-2 review sessions, creation of images for system operation, desired number of training sessions
How Is Standardization Delivered
Documented process flow with accompanying process instructions, operating instructions, training materials,informational materials, and possible E-learning.
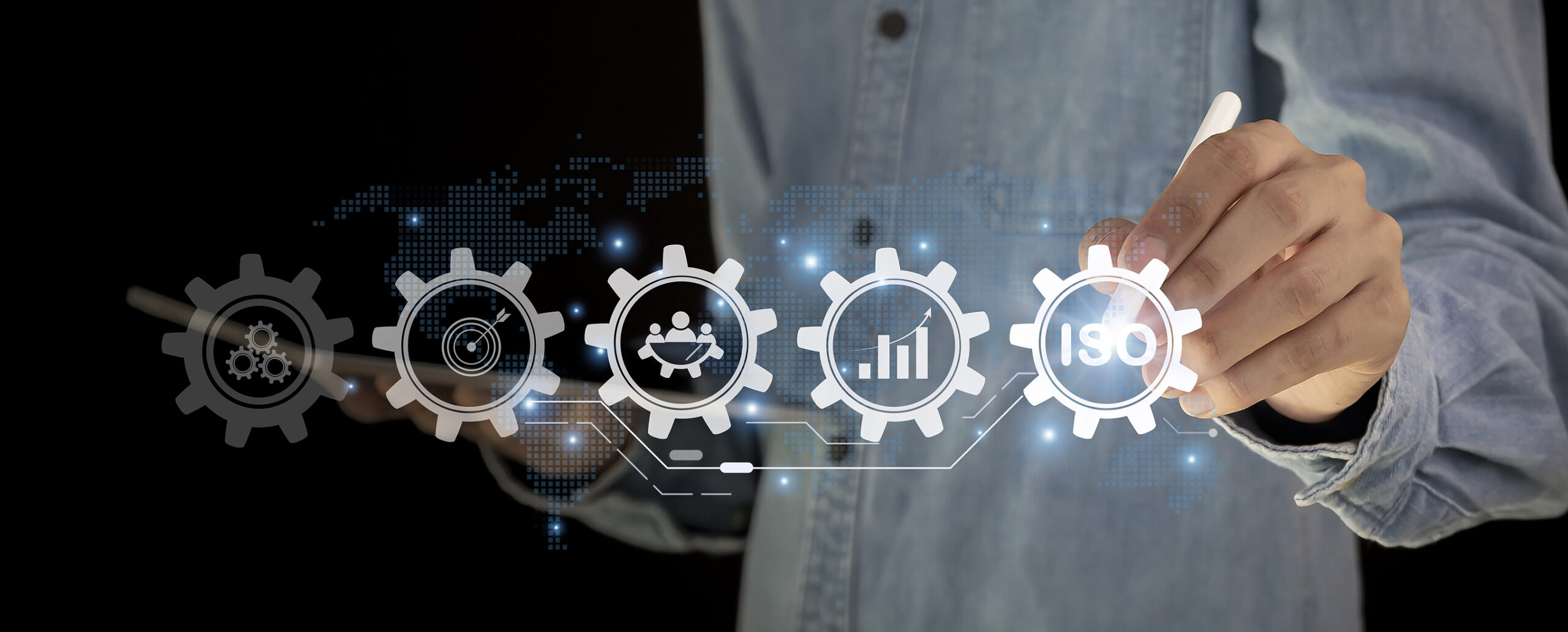
Contact Us
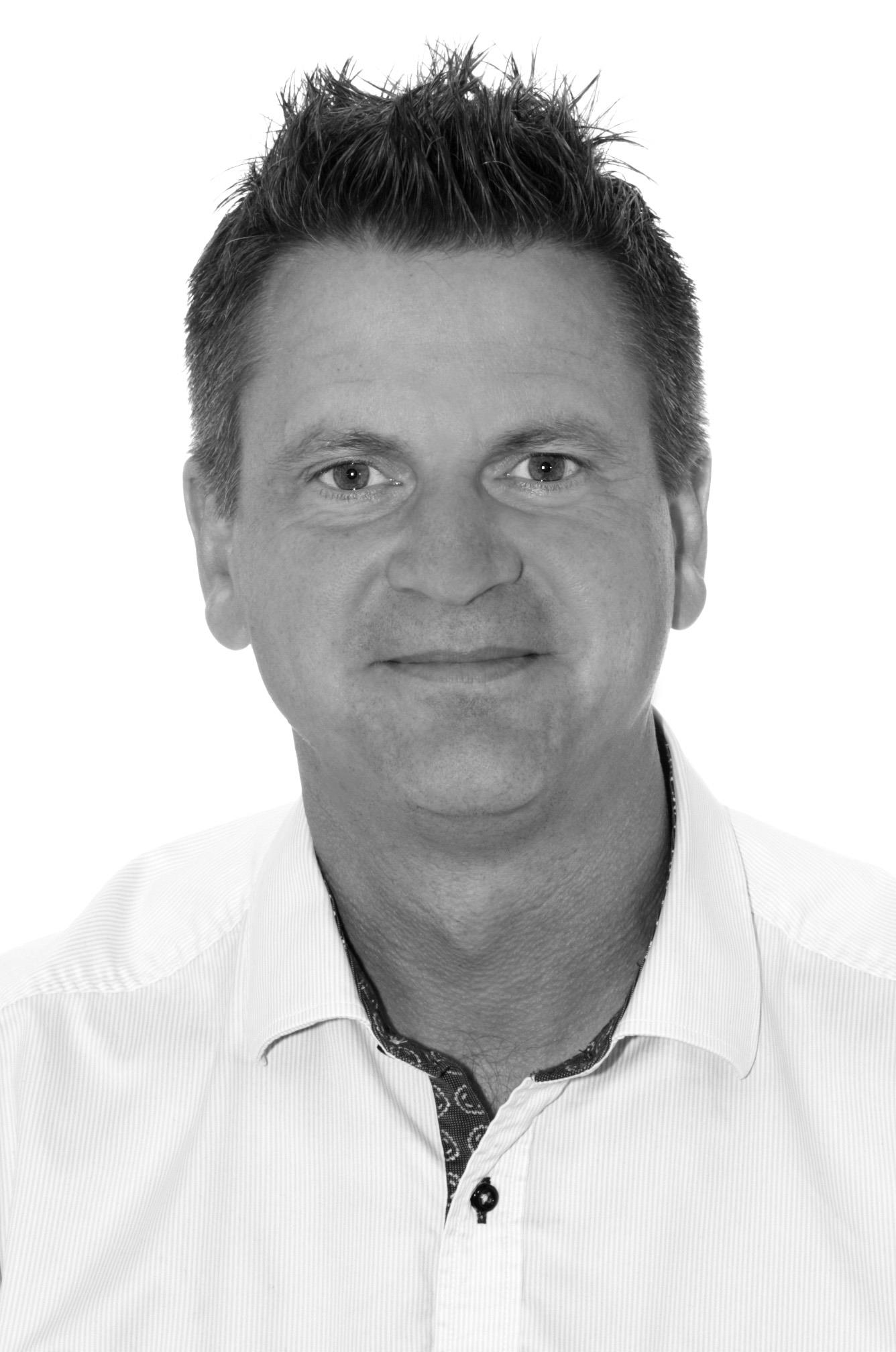
Håkan Östholm
Sales and Senior Business Consultant