APPLICATION IN MAXIMO APPLICATION SUITE
Visual Inspection
Home > Maximo Application Suite > Visual inspection
Maximo Application Suite - Visual Inspection
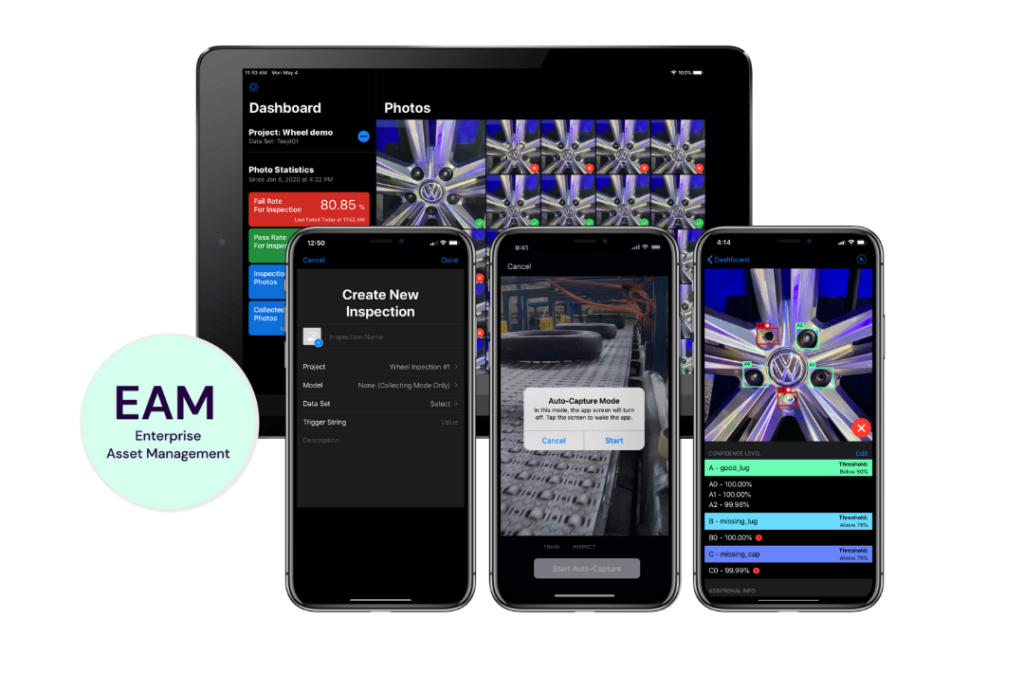
Visual Inspection enhances your ability to perform condition-based maintenance using cameras that detect deviations from expected condition levels. The camera can, for example, be mounted on a drone or temporarily placed on a stand near the area to be monitored.
Features
- Evaluation of image and video information
- Skapa modeller som kan distribueras via IoT, server eller smarta enheter
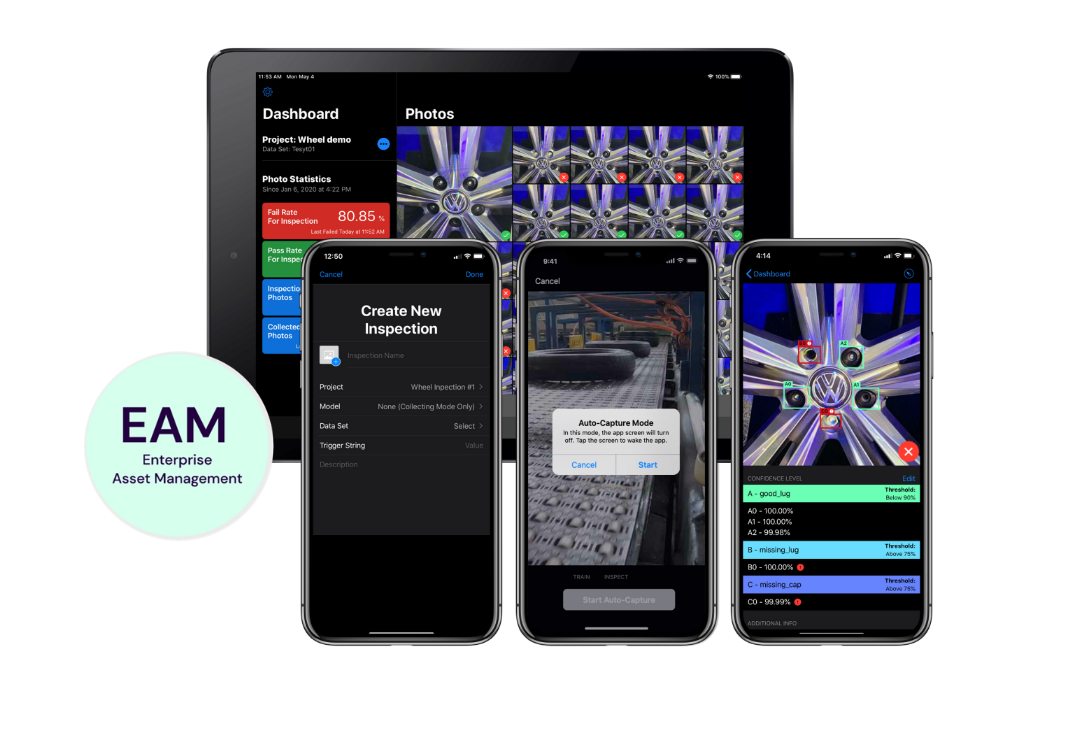
Take the Next Step in Your Maintenance Journey with AI
With Maximo Visual Inspection, you can let AI detect defects in real-time around the clock and alert the relevant maintenance personnel as needed. By creating and fine-tuning your own models, you ensure that these alerts are exactly as you wish. The graphical user interface makes it easy for anyone to go through this process, which involves preparing training data, training the model, and putting the model to work. Maximo Visual Inspection relieves your workforce and gives you full control over your most critical equipment.
Collect Data
The first step to get started with Maximo Visual Inspection is to collect images and videos that your model can then be trained on. If you want your model to alert when cracks are detected in conveyor belts, you simply need to collect images and/or videos showing conveyor belts in various conditions. Some of the material needs to show intact conveyor belts, and some need to show what a conveyor belt with initial cracking might look like. The point of data collection is to give the model a foundation from which it can independently determine whether a conveyor belt should be replaced or not. This material can advantageously come from previously conducted inspections.
Prepare Your Data
In order for the basic data fed into Maximo Visual Inspection to be meaningful for your model, the material needs to be labeled with tags. These tags tell the model what is what. An AI model rarely has trouble independently pointing out differences between images showing broken and intact conveyor belts, but at this stage, we need to associate the different variants with human terms, such as 'no cracking,' 'initial cracking,' and 'developed cracking.' By pairing these tags with the correct image or video in the basic data, we can then train our model to alert when cracking is detected and also specify the type. All of this is, of course, done in the simple user interface.
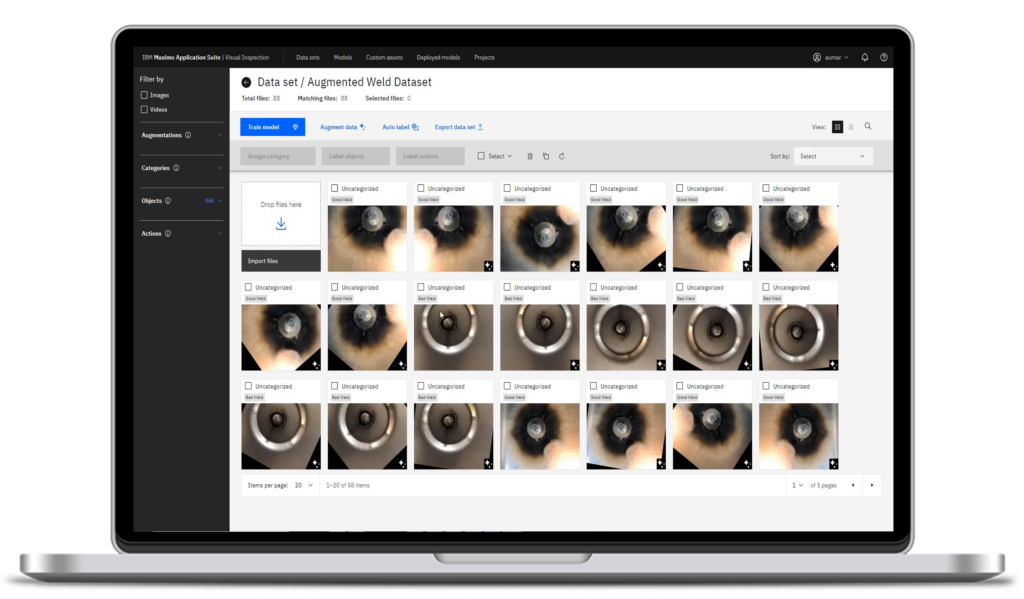
Train Your Model
After labeling your data with tags, it's time to train your model to alert according to your desired rules. You can do this with just a few clicks in the user interface. There are three different types of training to choose from: image classification, object recognition, and event recognition. Image classification pairs an entire image with one of your tags, object recognition identifies the presence of one or more objects and pairs them with tags, and finally, event recognition involves identifying a certain type of movement from a video, such as an object falling off a conveyor belt. If you are interested in detecting initial cracking in conveyor belts using regular still images taken from a mounted camera, image classification is a suitable choice. After selecting the training method, the model takes over and trains itself within a few hours, after which you have access to a controlled model trained on your own data.
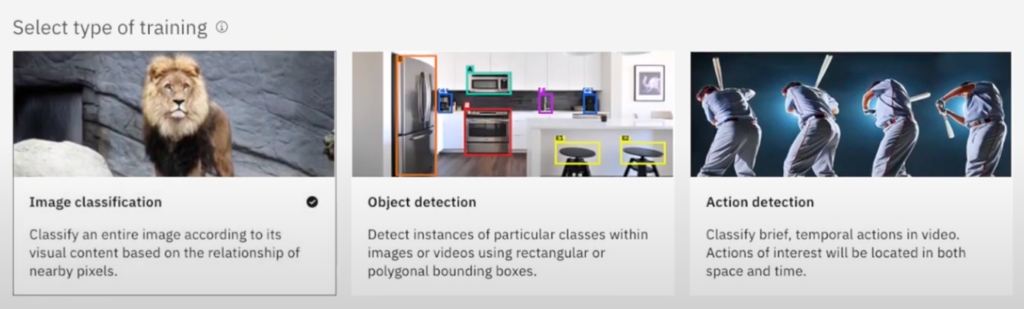
Put Your Model to Work
After training your model, you have the option to test your model and make adjustments to achieve your desired accuracy before proceeding to let your model work for you. Through Maximo Monitor, you can then view the latest results in a customized dashboard and allow your workforce to make decisions based on the model's continuous inspections. You can also set your model to create a follow-up work order in real-time when an automated inspection results in an alert. With Maximo Visual Inspection, you let AI help you and your business take your maintenance to the next level.